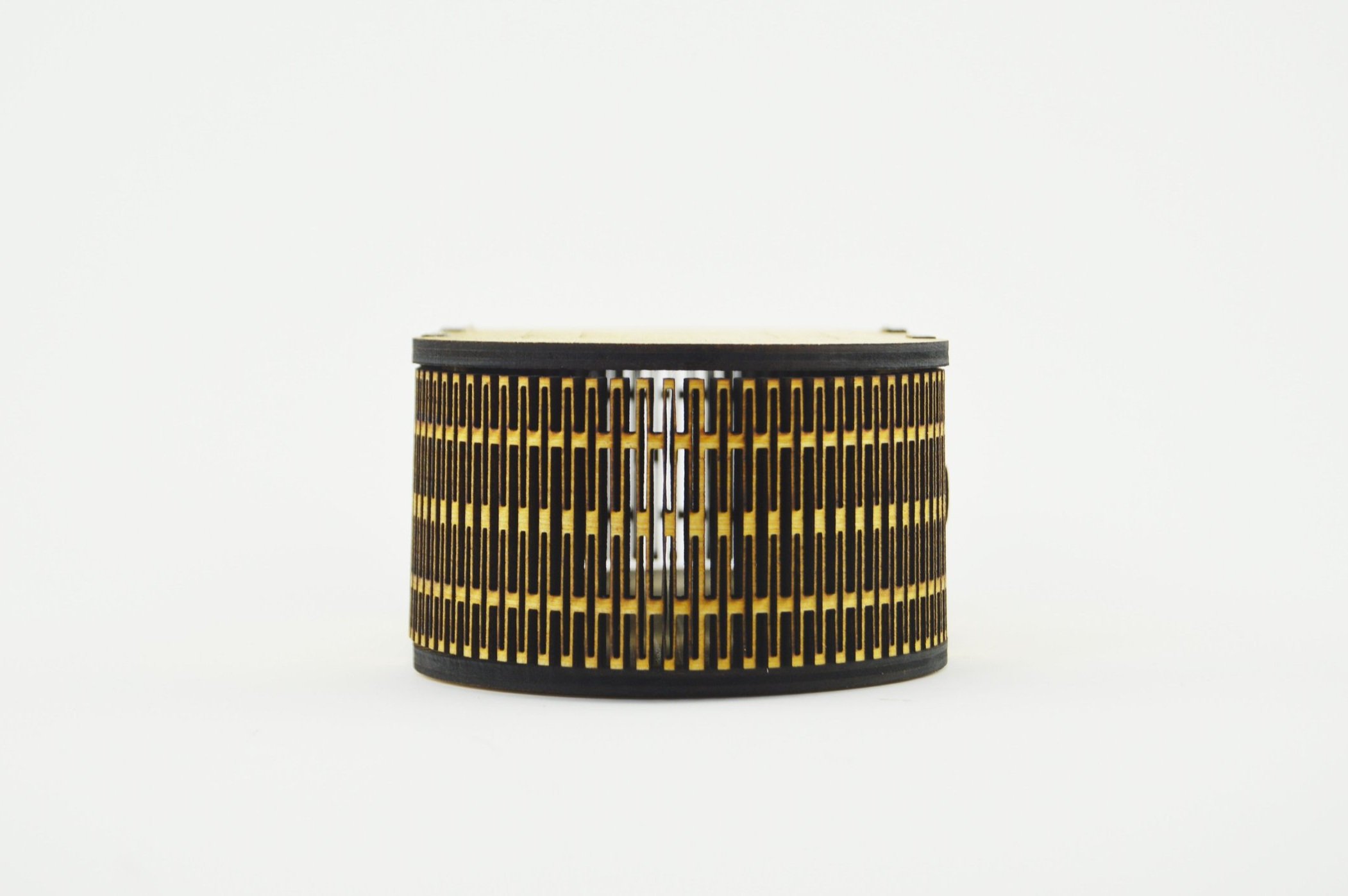
Unboxy Box
Assigned to reinvent the box, this project was an exploration of Rhinoceros 3D modeling and kerf cutting via laser cutter.
Designed in Rhinoceros (Rhino) and printed on PLS 6.75 laser cutter.
Ideation
My original plan of using only one piece of material and having the kerf cutting do all the work proved to be complicated quickly. I shifted gears after this initial design after learning more about kerf cutting & talking to the Digital Fabrication Studio coordinator.
Design
I constructed a 3D model primarily and then unrolled and used as the starting point for the 2D cut pattern. This series of screenshots from inside the Rhino software highlights my progression from original idea, to secondary idea, then on to the flat lay of the cuts that needed to be made (first and second iteration).
-
Kerf Cut Trial #1
The first attempt proved to be on the right track but had all the pressure on one point in the pattern. This in conjunction with the steep curve caused the material to snap.
-
Kerf Cut Trial #2
Attempting to create an overall more flexible form, I moved to a drastically different pattern. During this trial I realized that different kerf cutting patterns have the ability to bend in different directions more easily that others and this pattern actually did the opposite of what I was aiming for.
-
Kerf Cut Trial #3
Success was achieved on the third trial of kerf cutting patterns created. This attempt, I went back to the original design, consulted peers, and created a design better suited to the curve, adjusted for a less intense bend needed, and distributed the points of pressure across the pattern.
First Iteration
Before finalizing my model, I designed and cut a first iteration to see what adjustments needed to be made. This model helped me understand the intensity of laser needed, how to avoid burn marks, strengthen my kerf cutting, and create a stronger final piece.